ESG1 Cogeneration Series
Exhaust Steam Generator
Full Operating Steam Pressure from a Cold Start in Less than 10 Minutes.
The fully packaged ESG1 (Exhaust Steam Generator) is selected from 124 pre-engineered standard models with output capabilities of 20 to 300 boiler hp and operating steam pressures from 3 to 450 psig. The ESG1 is shipped complete, ready for operating as either a primary or supplementary steam source.
The ESG1 package is made up of three basic sections:- Finned tube heat transfer section
- Steam flash circulating drum assembly
- Modulating full port exhaust bypass system
Engine Exhaust Application
Capacity: 400kW to 7MW
Entering gas temps: 500°F to 1,250°F
Heat Sink Types: supplemental steam demand and/or primary steam source for steam heating or process steam
Operation and Control
The integral forced circulating water pump continually circulates high temperature water from the steam flash drum assembly to the heat transfer core assembly. BTU is transferred from the exhaust to a high flow superheated water/steam mixture. The superheated water is returned to the steam drum which contains dry pipe, baffles, and lance assemblies, where it flashes into 99% dry stream as its exits out to the system.
As the water is generated into steam and exits the boiler, the modulating boiler feedwater system controls continuous feedwater flow for constant drum water level control. Fail safe controls are built in for full exhaust bypass in the event of electrical or pneumatic loss.
The steam pressure controller maintains the operating steam pressure as it controls the modulating exhaust bypass assembly. This provides solid operating steam pressure under various operating steam load demands.
Quality Control
The ESG1 is manufactured, tested, and stamped in accordance with the requirements of Section I of the ASME Boiler and Pressure Vessel Code, and National Board. Boiler trim includes all safety controls and alarms to meet state and federal codes. Final assembly, electrical wiring, and factory adjustments are completed under a strict set of guidelines.
The ESG1 is an easy choice when compared to the"old technology" of a conventional firetube boiler:
- Completely self-contained package design reduces engineering, installation, and maintenance costs.
- Size requires only 1/2 the floor space and 1/2 the weight of conventional boilers, which reduces building size, structural support costs, and shipping costs.
- Ease of tube replacement requires no overhead cranes, special rigging, special crews, or extra roof height above the unit, while reducing down time.
- Many shapes and sizes are available to fit limited space and maintain performance requirements.
- Produces greater than 99% dry steam.
- Provides 100% turndown capability.
- 5–10 minutes from startup to full output.
- Integrated exhaust modulating bypass for safe automatic steam control.
- Explosion-proof heat transfer exchanger.
- Low friction loss for minimum static exhaust back pressure.
- High circulating flow to minimize scale buildup.
- No thermal expansion concerns with cold boiler feedwater.
- Performance aimed at the lowest pinch point in the industry (final leaving exhaust temperature minus operating steam temperature) for maximum thermal efficiency.
The ESG1 requires only the following connections for a cost effective installation:
- Steam Outlet
- Exhaust Flange Inlet and Outlet
- Single Main Power
- Single Main Blowdown
- Feedwater Inlet
- Pneumatic Control Air
- Cooling Water Inlet and Outlet
ESG1 Optional Components
Continuous Blowdown with Intermittent Conductivity Sampling Assembly
Maximize boiler efficiency by periodically sampling surface blowdown water and controlling total dissolved solids. Maintaining optimal levels of concentrations will control the costs of water, energy, and chemicals. Assembly includes: motorized valve, probe and piping assembly.
Automatic Sootblower
Sootblowers are available either as a manual push button start or fully automatic with timed sequencing. Sootblowers are considered when firing with fuel oil and/or incomplete combustion. Sootblowers are also considered when manual cleanings are not feasible in order to maintain peak performance.
Hinged Access Door for Full Heating Surface Inspection
Hinged access doors are considered when firing with fuel oil and/or incomplete combustion requiring full access on a regular basis for manual cleaning. A hinged access door can be incorporated for 100% finned tube viewing and attention.
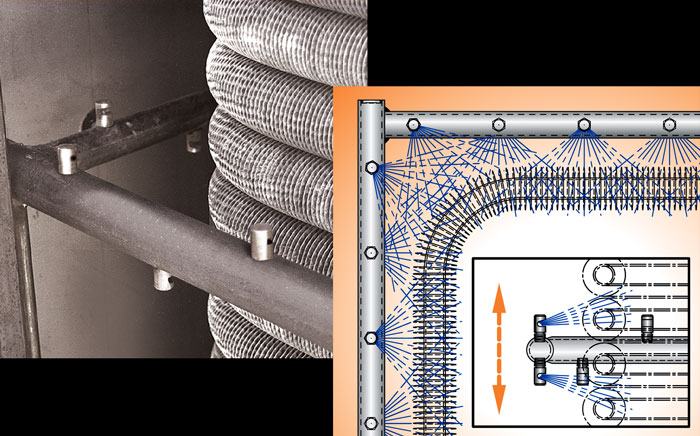
Automatic or Manual Sootblower (optional)
The exclusive Cain Industries Timed Automatic Sootblower design is applied to combustion sources where the sulfur content is high and/or combustion efficiency is poor. When a soot layer accumulates on the heating surface to a thickness of 1/8", fuel consumption is increased by 8.5%. The sootblower is also applied when it is not cost-effective to open inspection doors and clean the exchanger by other means. The sootblower system will continually keep the heating surface at a high performance level and eliminate the day-to-day operator expense and engine down time.
The blowdown sequence occurs while the engine is in full operation and is fully adjustable. The special flood-jet type nozzles achieve maximum cleaning velocity using steam or air as discharged through an electric control valve (included). Together they form a "continuous knife edge concentrated spray pattern" surrounding the heating surface. This "ring nozzle assembly" as attached to a manifolded flexible steel hose assembly, is powered up and down by a pneumatic drive cylinder. Dual timing relays allow complete control for 30 second cycle duration and intervals specific to each application. Final results are controlled double cleaning action, insuring that the maximum BTU recovery and anticipated savings are achieved.